

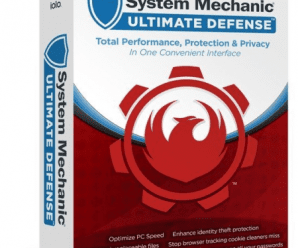
Many papers have been published on methods to determine the normal spring constant, kz, of atomic force microscope (AFM) cantilevers. The accuracy of the developed testing system is -17.5 % to 12.7 % of the measurement error compared to the torsion beam spring constant obtained from the resonance frequency, and -15.6 % to 7.2 % compared to the theoretical calculation value, thus verifying the effectiveness of the proposed test method. The torsional spring constants of test samples were obtained and compared by three different methods: a testing system using this principle, a resonance frequency method, and a theoretical calculation. The proposed method can maintain the load detection axis of the load cell and the lever part at almost a right angle regardless of the degree of torsional angle, preventing slip at the contact point between the load cell and the lever part. As a method to reduce the sliding force, we proposed to generate pure torsion in the torsion bar section by rotating a sample holder with a test sample attached. In the push-in method, the sliding force increases as the indentation amount increases, decreasing measurement accuracy. The push-in method is used to measure the mechanical properties of these micro torsion bars, in which a lever connected to the torsion bar is pushed.

MEMS scanners use micro torsion bars made of single crystal silicon.
